In Consteel 18, we’ve dedicated significant effort to enhancing every stage of the structural modeling, analysis, and design process. From improved onboarding to enhanced collaboration with colleagues and ensuring smooth integration with other software, we’ve focused on making substantial progress in usability, scripting, and engineering features. Additionally, we are excited to unveil the first version of our long-term development project: the FALCON plugin, a comprehensive wind load generator tool based on fluid-dynamics simulation. Let us introduce the new features of Consteel 18!
Onboarding
New Project Center
We have completely renewed our Project Center, the central hub for accessing Consteel, and the key area for managing and organizing your models. The goal of this development was to create a seamless and tailored flow for navigating the various expanded model management options. The two basic options are clearly separated with extended alternatives offered:
Creating a new model:
- Start from scratch with an empty model
- Build a parametric model quickly from the new Parametric Models Library
- Import a model in another format (IFC, Smadsteel, SAF)
Opening an existing model:
- Browse files on your local computer.
- Access models from your cloud storage
- Select from your recently saved models
- Choose from the new Example Models Library
- Explore the new Tutorial Models Library
Moreover, in the new Home view, the offered model management options are customized based on the profile and workflow type of the logged-in user. You’ll also find a personalized feed of news, release notes, bug fixes, and additional content, along with information about your current software license.
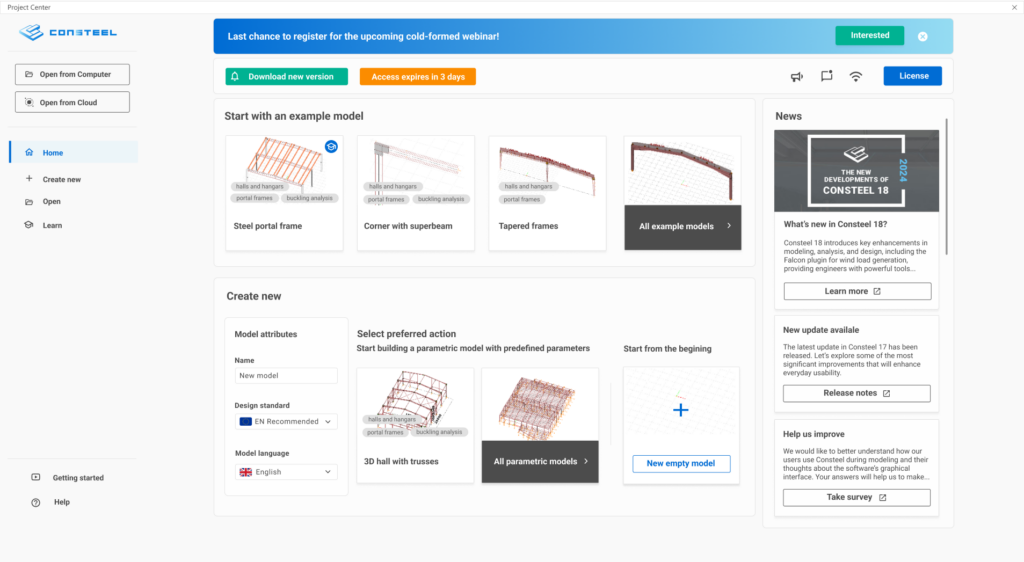
Navigation overview
A new onboarding feature has been introduced to assist our new and existing users with a comprehensive set of information, and settings regarding the model navigation options in Consteel. When you create or open a model, the Navigation overview window will appear, providing detailed information on navigation, selection, model views, background settings, and help functions. Each description is enhanced with animations to ensure clear understanding. You can also customize your navigation preferences — such as movement, rotation, and zoom — by choosing from settings used by several popular software platforms. The window can be called up at any time from the Help menu.
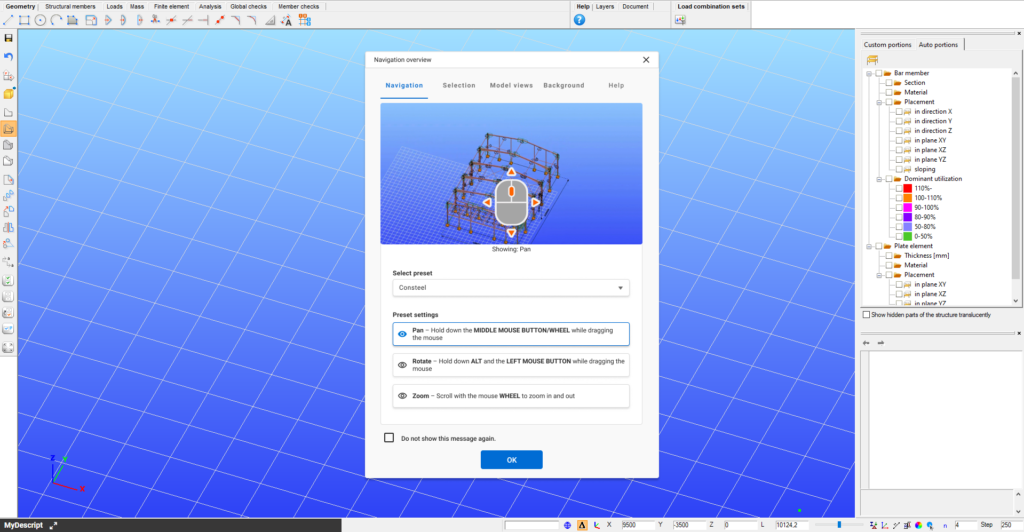
Collaboration
New Import Center
Interoperability between different software models is a more and more crucial problem for structural design offices. At Consteel, we continuously research the most important ways of model transfer to support them with our model import and export functionalities. In Consteel 18, we put all these functionalities into the new Import Center area helping you to coordinate between your models of different sources and unifying the model import workflow.
The process begins by displaying all your models with importable file formats in the selected folder. You can use the preview feature to quickly view compatible models (.ifc and .smadsteel) in a pop-up visualization window. Once a model is selected, a generalized model conversion is initiated (see next function), generating a Consteel-compatible model that can be positioned in the workspace. A comprehensive log provides a detailed summary of the conversion process.
Generalized model conversion
In Consteel 17, we began laying the foundation for a unified approach to converting imported models using our general format (.smadsteel), which is compatible with both Consteel and Steelspace. The first application of this was the successful conversion of AxisVM models. Now, we’ve further advanced this technology and extended it to support the conversion of IFC and SAF models as well.
During this generalized model conversion process, cross-sections are converted through a multi-level method. First, a user-defined tabular conversion file is used to match cross-sections by names. If no match is found, a name-based search is conducted in the Consteel profile database. Finally, if the search is unsuccessful, the cross-section is created using the parametric section macro defined in the source model. The detailed logging also developed further, providing information about the values of both source and target attributes in the converted objects. The log includes comprehensive details on any deficiencies, errors, or warnings encountered during the conversion.
Cloud collaboration developments
We strongly believe in the power of cloud tools, particularly for collaboration, accordingly, we are continuously improving our Steelspace platform. In this version, we introduce a multilevel commenting tool for cloud-saved and shared models. Comments can be linked to individual model elements, specific model parts, or the entire model. All participants (whether owner or contributor) are notified of any comments made.
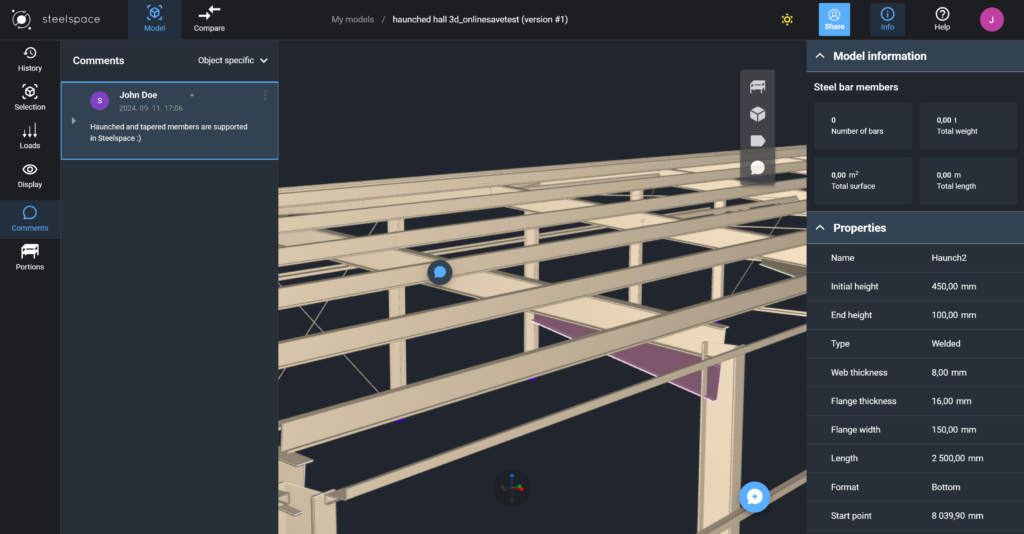
Software use
New Documentation Center
Comprehensive documentation is crucial for the effective use of any software, and we’ve addressed this by transforming our user manual into a fully integrated Documentation Center. Previously focused on Consteel and Descript, this new platform now consolidates the Consteel manual, Descript manual, Plugin documentation, and Release notes into one centralized resource.
The updated platform introduces several enhanced features, including a dark and light mode for a customizable viewing experience, advanced search capabilities to quickly locate relevant information, and support for multiple software versions. These improvements make it easier than ever for users to access the precise guidance they need, tailored to their preferences and software version, resulting in a more seamless and efficient workflow.
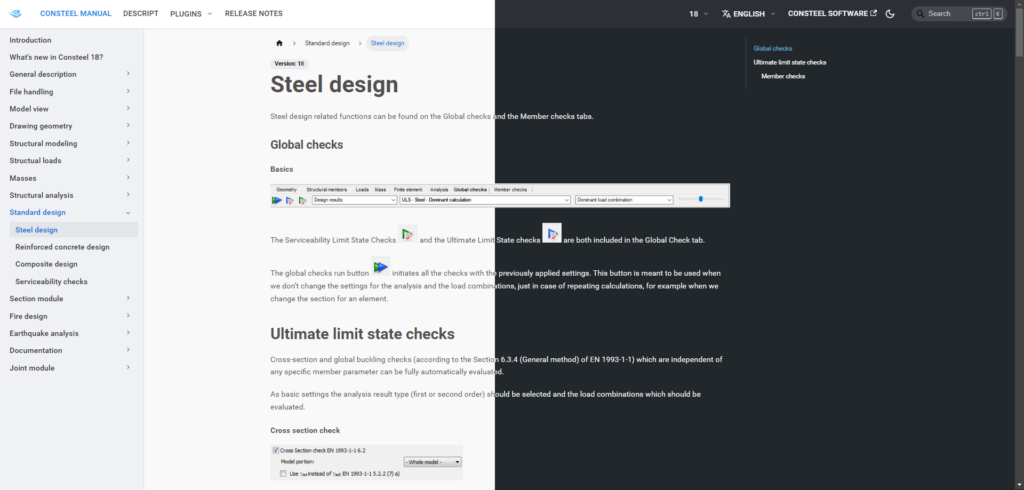
Cross-section handling
We’ve introduced a new method for managing steel cross-sections and profiles, offering greater flexibility and efficiency. You can now create a personalized section library that includes your frequently used sections—whether they are standard, macro, or manually drawn—and organize them within a custom folder structure. This library is saved locally on your computer, allowing you to quickly access your preferred sections across multiple projects.
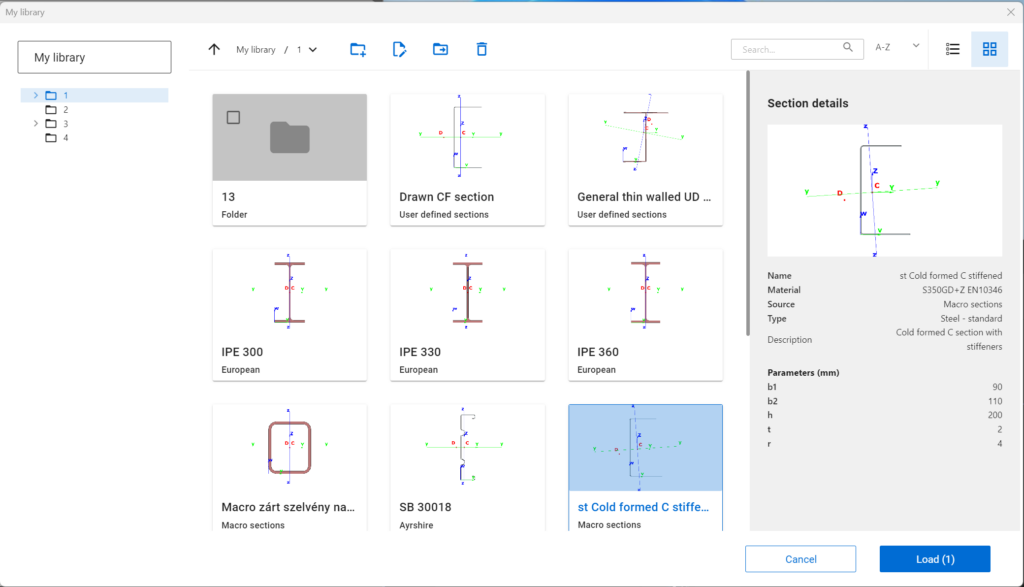
Descript improvements
Parametrizing models and workflows can greatly streamline many everyday tasks, a benefit increasingly recognized by our users. In response, we regularly update our scripting environments to enhance efficiency. In Consteel 18, in addition to the new Descript functions added to our library, you’ll find entirely new user interface components within dialogues created by scripts. These updates are designed to make your scripting more intuitive and effective.
Cloud model handling
Our Steelspace platform has seen several upgrades in its cloud-based model viewer and management functions. The viewer now supports visualization of tapered and haunched members from Consteel models. Additionally, custom model portions can be accessed within Steelspace, allowing you to view these portions alone or with a transparent overlay of the rest of the model. These enhancements provide greater flexibility and clarity in managing and reviewing your models.

Engineering developments
New structural member object: member with double C profile
As a high-level software solution provider for steel structural design, we are committed to advancing the field of cold-formed steel. One of the most commonly used structural elements in this sector is the member with a double C (or Sigma) profile, valued for its relatively simple manufacturing and structural efficiency. However, as it is always the case for cold-formed members, the mechanical behaviour and its accurate analysis and design is far not straightforward.
Our new structural member object addresses all these complex challenges. It accurately calculates all properties, warping and torsion effects, and buckling modes associated with the double C profile. The member performs standard design checks on each individual section, all while simplifying the modeling process by integrating both sections into a single member object.
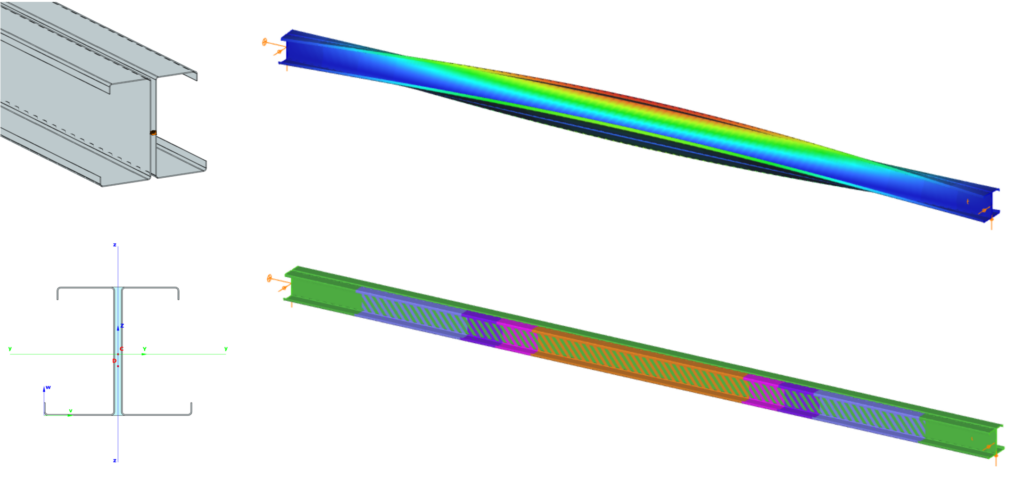
New support type: compression-only support
A new point support type is introduced : the compression-only support. This support involves an iterative process during the first and second order analysis to find the real state, similarly as the tension-only element. With this support you can model situations when there are no real connectivity between objects they merely rest on each other.
The FALCON plugin
In recent years, we have invested considerable effort into researching and developing ways to utilize CFD (Computational Fluid Dynamics) simulations for generating wind loads on buildings with non-standard geometries. From the very beginning, our primary goal has been to provide a transparent and intuitive tool for practical engineers, ensuring that the application process remains as straightforward as traditional wind load generation methods.
Accordingly, the focus is not on the simulation process itself, which serves only as an internal tool to assist in the generation of wind loads. Instead, our emphasis has been on post-processing the simulation results, offering a wide range of methods to automatically generate the familiar wind zones and load objects. These outputs align with standard solutions, making them easily understandable and reviewable by engineers.
While this approach represents a modern and innovative method for modeling wind loads, it is relatively new to many engineers. To facilitate widespread adoption and understanding, we aim to build consensus and foster acceptance within our user community. To this end, we are introducing the FALCON plugin in Consteel 18 as a free Beta version. This allows for preliminary testing and feedback. Following a calibration and fine-tuning phase in collaboration with our dedicated users, the final version is set to be released next year.
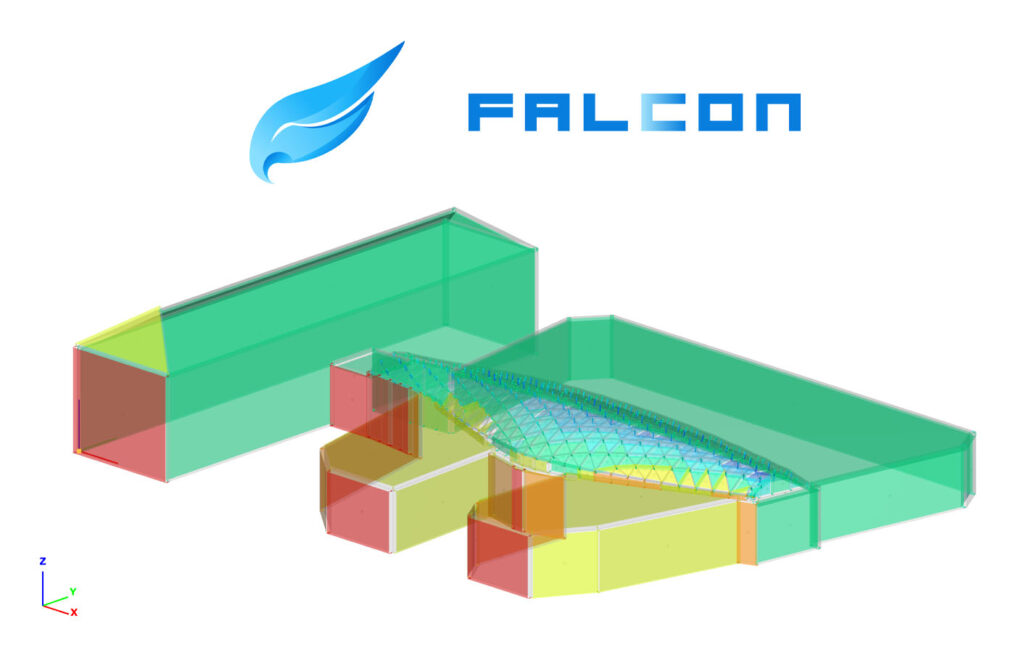
Webinar recordings on the developments of Consteel 18 and the FALCON plugin are now available on our YouTube channel.
Part 1 – Software licensing
Due to the radical growth of the use of software products in every part of our life the licensing options have been significantly changed and developed to handle all the different needs. As we have also been growing and expanding our services, we had to rethink what values we want to deliver for our clients and how we can provide and sell them most efficiently. From the release of Consteel 15 we start to gradually reform our licensing system, this article provides the background and directions of this process.
Our services are still built around our core software solutions so the structure and conditions of how to use them are defined primarily by the licensing system. On the other hand, we provide an increasing amount of various supplementary services to our users – from support and training materials through modern scripting options to collaborative online services.
We strongly think that these services are very important components in creating an efficient structural design workflow around our software solutions.
Finally, the demands and possibilities of how to access the software and the services have also been significantly changed and the pandemic times showed a couple of new remote and collaborative working modes.
We would like to present our answer to all of these issues so the article is divided into 3 parts showing
- (1) our new licensing model,
- (2) delivery of our supplementary services and
- (3) our new accessing model.
This first part deals with software licensing.
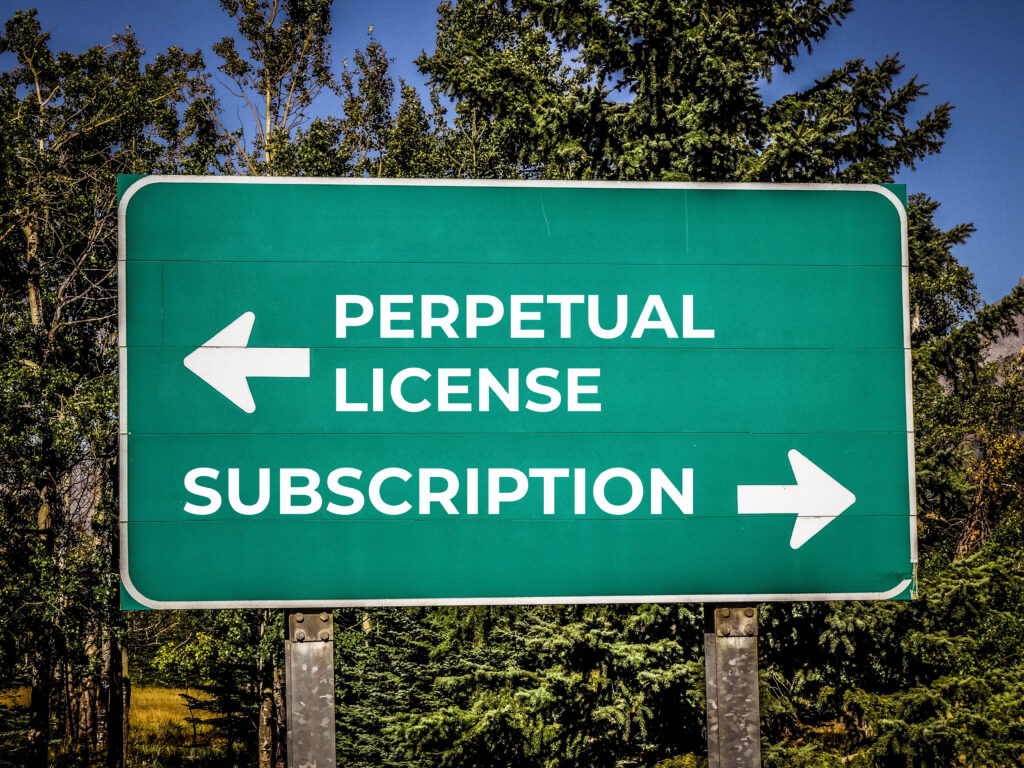
Perpetual license or subscription
Perpetual licensing is the most traditional software licensing model, it has been and is still used by most of the structural design software vendors including us. In this model, the customer purchases a software license once and keeps it forever.
However, first it should be noted that no real perpetual license is existing.
This has been the case in the past, but it is especially true today. This is because no single software product can be used on its own without a number of special software and hardware requirements. The most important ones are the certain type and version of operation system, processor, memory, display system, resolution etc.
Having seen, however the rapidly changing software and hardware technology the purchased version of the software can operate only during a small time slot while the original conditions are available. The more and more frequent updates in the operating systems (especially regarding data protection), the applicability on the quickly developing desktop computers with high-resolution screens as well on novel laptops and notebooks requires continuous upgrading of the original software version to ensure the constant level and bug-free operation.
Accordingly buying a perpetual license for a particular version of a software without subscribing to software updates results only a limited time of efficient use. The classic subscription system, where the use of the software is subject to continuous, periodic payment, can be a solution for this problem since the user can always access the latest versions.
However, the payment of the perpetual license together with continuous software upgrade is nothing else than a special kind of subscription where a larger initial payment is followed by moderate amounts of periodic fees. It can be concluded that a perpetual license without continuous upgrading makes problems for the developers and the users as well,
so the subscription type of software licensing seems more appropriate to today’s demands.
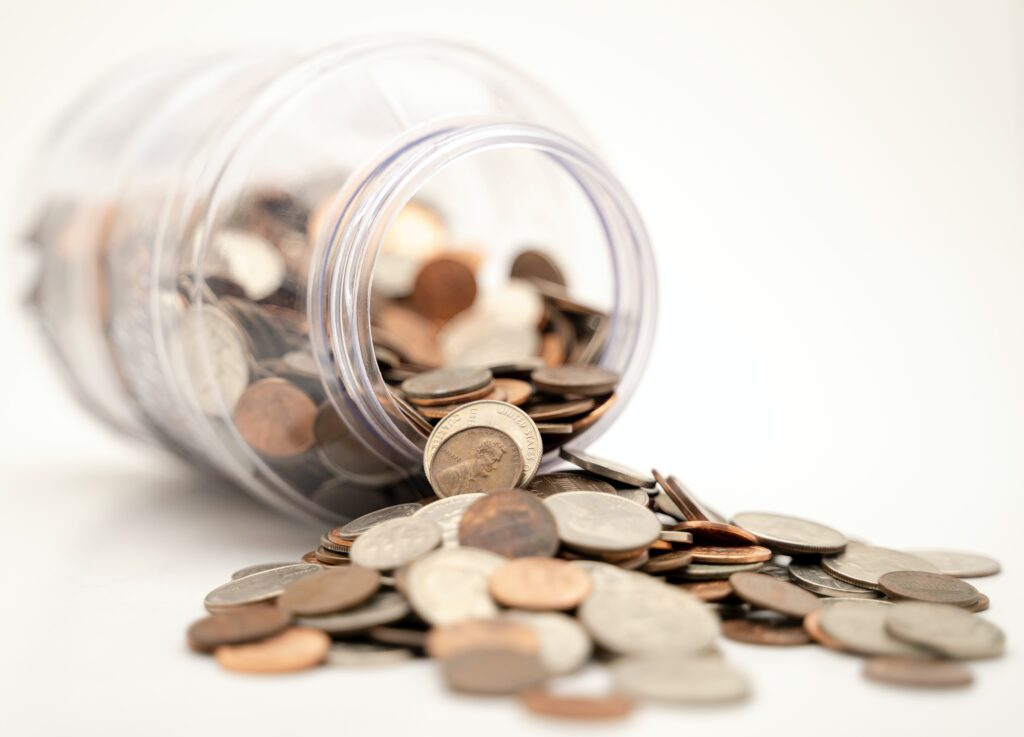
Company investment or project cost
The structure of payment for software licenses can be analyzed from another point of view as well. In the operation of a company the purchase of a software license can be regarded as two different cost types:
- (1) an investment cost with the aim of strengthening the overall profile of the company
- (2) a project cost with the aim of providing an efficient tool for a certain project
Even the accounting is different for such costs, but also the payment structure must also adapt to these different situations. In the first case, the software is considered as a basic tool for the long-term operation of the company, serving continuously their core business. They build their workflow on the software; they are seeking employees with skills in that software etc. Moreover, an initial investment with a larger amount of cost could also be justified by several forms of grants supporting the procurement of software tools of the company.
In the second case, the software is planned to be used only within a short period of time generally connected to a specific project where the software can be a necessary tool. The company does not plan with the use of the software beyond that project, and it is not an essential tool for their core business or day-to-day workflows.
It is obvious that in the first case the suitable solution is a perpetual type licensing model where the initial investment is a one-time license fee followed by the moderate additional yearly upgrade fee. This solution is less sensitive to possible fee changes, and the initial investment can be amortized or supported by external sources. In the second case, the periodic (generally monthly) subscription is a better choice.
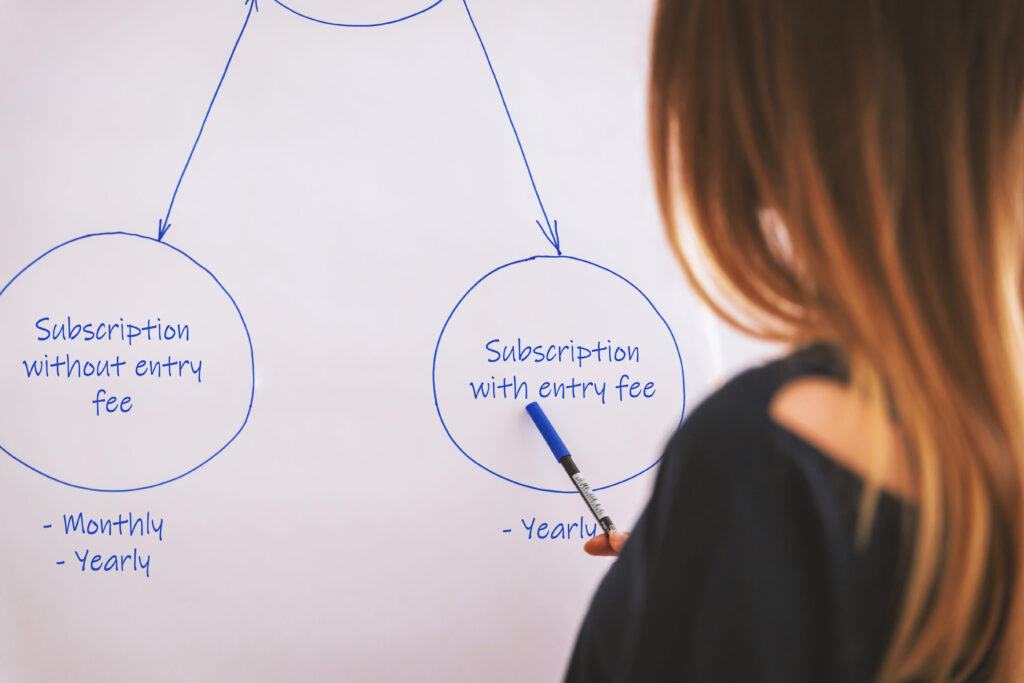
Our new licensing solutions
First of all, the perpetual license type will gradually be phased out from our licensing model, and we are going to switch completely to subscription. However, we would like to offer a solution for both of the cost options presented in the previous section. Accordingly, besides the well-known subscription type with equal periodic (monthly, yearly) fees we introduce a second subscription possibility as follows:
Model A. Subscription without entry fee
Classic subscription model with periodically billed fees of equal amounts. The subscription can be ended and restarted at any time. Ideal for project-based software use. Two types will be introduced:
- A1. Monthly subscription
- A2. Yearly subscription
Model B. Subscription with entry fee
A modified subscription model where the first, entry fee is a larger amount followed by an equal periodic fee term with significantly lower fees compared to Model A. The subscription can be paused with special conditions (see later). Ideal for company-based software use. Only yearly subscription is available.
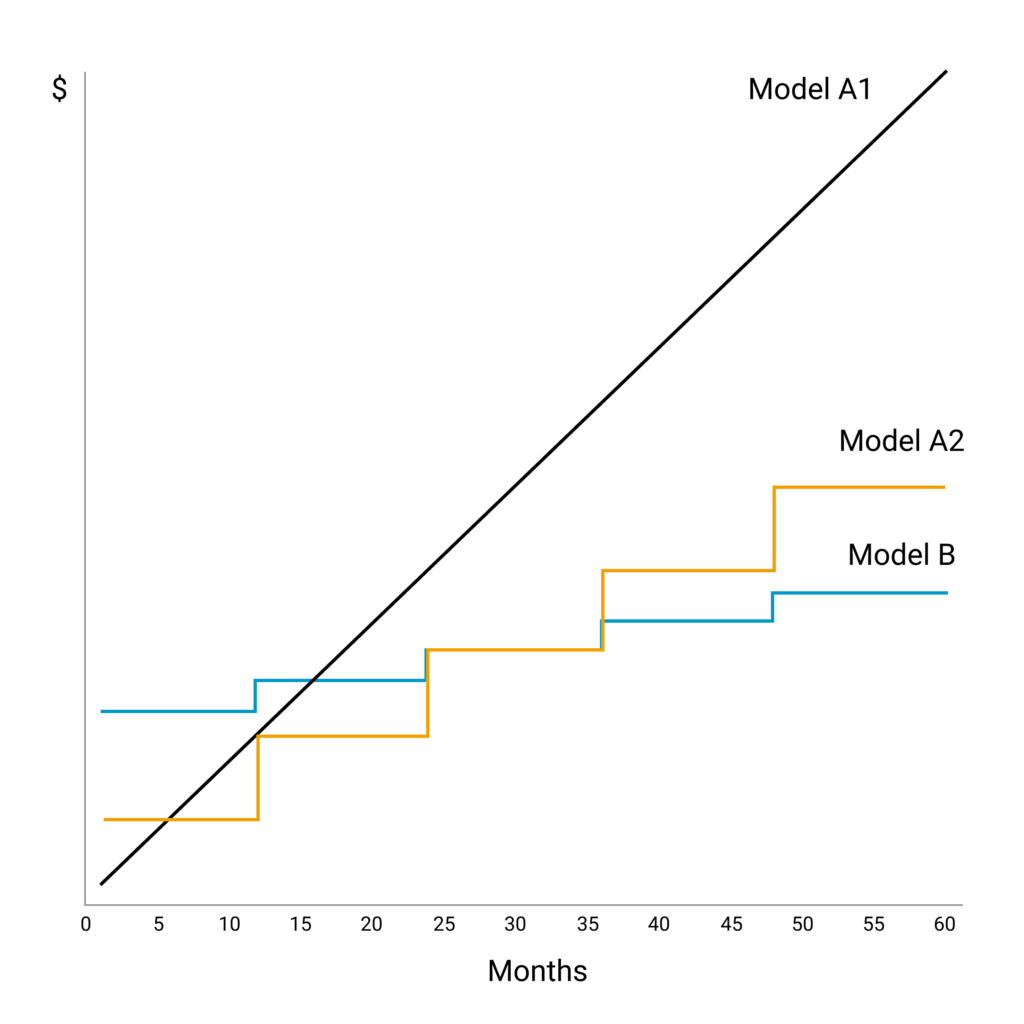
Since the two models serve substantially different business models it is important to note that there is no possibility for switching between the two licensing models.
In the following, some additional licensing aspects will be briefly discussed.
Multiple seats
In software licensing models there is traditionally some discount policy for multiple users or more exactly for companies buying software licenses with multiple seats (possibility for parallel access for more end-users). This is a good and legitimate tradition given that the extra seats do not represent an extra cost for the software producers. In our new licensing model this quantity discount will be available for both versions with the same percentage. For Model A2 and Model B, the discount goes to multiple seats in one license with the same renewal day. Accordingly, new seats with subscription fees reduced by quantity discount can be added to the license at any time but the renewal date will be the same as for the earlier seats. For Model A1 the quantity discount rate is based on the summa number of seats in the license at the beginning of the period. In this way, new seats with the full-length monthly subscription (Model A1) can be added to Model A1 and Model A2 as well at any time.
License intermission
Although for intermittent software use the Model A is recommended, it can happen with companies invested in subscription Model B that the software is out of use for a certain period. In this situation, the license can be paused for up to 3 years not paying the yearly fee. Within this timeframe return to the license with the same conditions is allowed. However, after 3 years of license intermission, the license will be lost, the return can be done with a completely new license only.
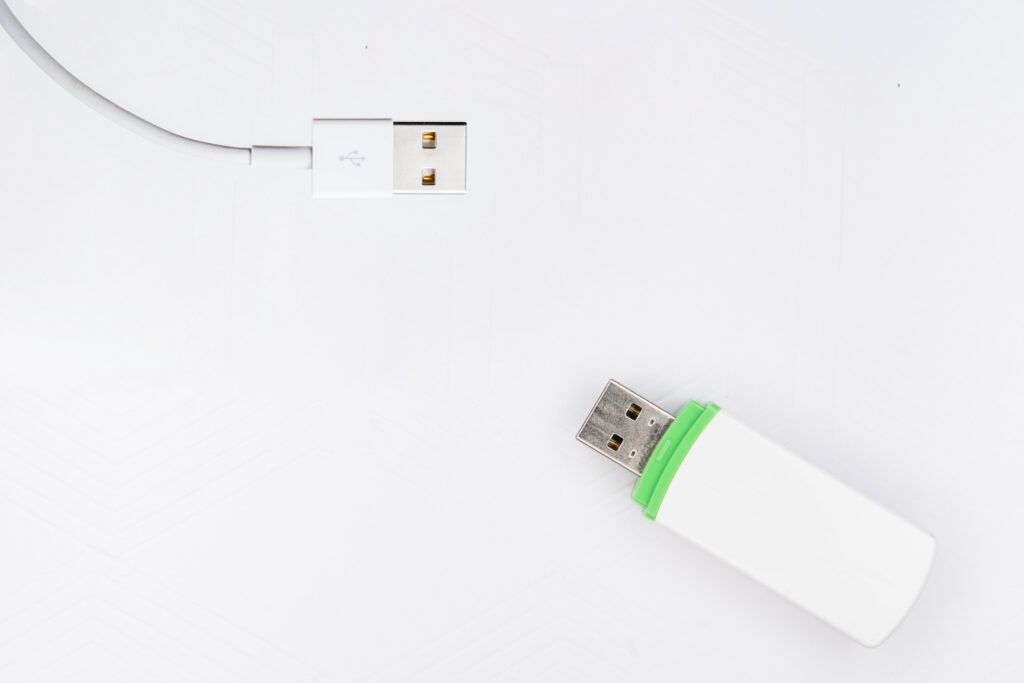
License protection
There will be two types of protections available for the Consteel licenses: the usual hardkey (single and network) or the online protection. The online protection type is relatively new for Consteel users, but it is an own developed, very flexible, and comfortable tool for any licensing option, so we strongly recommend switching or choosing this type of protection. In the brand-new online license administration tool, the software seats, accesses, and end-user permissions can be easily managed, it will be presented more in detail in the third part of this series.
Introduction
The workflow of engineers during the structural design process is rapidly changing nowadays. This change is mainly caused by the quick development of the engineering software tools which are trying to cover practically the entire design process. There is also an intense specialization direction of the developments, where more and more efficient software solutions are offered for more and more narrow and focused design phases. It creates a new situation for those design offices, trying to keep up with the technologies and increase their efficiency, that usually have several software tools for the different phases of their design workflow. However, the use of the most competent software for a certain phase is just one side of the coin, the whole process can only be efficient if these phases are suitably organized and connected. Theoretically, this is covered by the BIM approach, practically it highly depends on the quality of the interfaces between the different software tools. The optimal workflow is, however, not obvious even for a certain project, it is further influenced by several parameters like the size of the design office, the experience of the engineers, the local structural design regulations etc. Accordingly, it is still a far goal that a standardized process can unambiguously guide and govern the most efficient way of structural design processes. That is why it can be quite interesting to survey the recent situation, to find out how the engineers are actually working.
We made a survey asking more than 100 users of Consteel software from 6 countries (Hungary, Poland, Greece, Germany, Spain, Romania) about their typical structural design workflow. In the followings we present the results of this survey, discussing the model creating (geometry, model import, mechanical objects, connections), result exports, working model exchange and final model export issues.
Respondents
All the respondents are Consteel users, and the answers reflect their workflow in the structural design of various steel structures. The figures below show the characteristics of the respondents in terms of company size, project type, Consteel seniority.
It is important to see that one-third of the respondents are very small or one-man companies, and the majority is from small or medium-sized companies. Most of the works are industrial projects (halls, industrial buildings) with some public and technology projects. Most of the respondents are proficient or experienced software users, some of them are starters.
Modelling the main structure
The creation of a global structural model suitable for the basic mechanical analysis and standard design calculations consists of two main phases:
- modelling the geometry of the real structural members with cross-sections, lines (beams, columns), surfaces (plates, slabs, walls)
- and definition of the abstract additional mechanical objects which are not part of the usual BIM model – loads, supports, connectivity of the structural members, eccentricities, dummy mechanical elements etc.
The results of the calculations on this global model are usually supplemented by additional structural design details such as connection design, foundation design etc. These design issues are generally performed by specialized software tools, the fit of the models of these tools into the whole BIM process is also an issue.
Starting with the geometry modelling the next figure shows the ways of creating the main geometry in Consteel. Half of the respondents do not use any import possibility and build the whole geometry in Consteel from scratch. Although the direct modelling is apparently still dominant, there is a considerable number of users applying the model import functionality and starting the modelling with receiving an existing model. Moreover, 10% uses only the model import, they probably created an efficient workflow for the model management where the model creation is done in a specific external (maybe parametric) software tool.
The next figure shows the types of software tools where the initial structural model import comes from. These tools are dominantly detailing, architecture or simple drawing software products. It is important to note that the detailing and architectural tools can provide much richer information about the model than the drawing software which usually yields only the line wireframe. But it is a very good sign that 4% of users create the initial model by scripting using some parametric software tool, this method can be regarded as a very advanced end efficient workflow for model management.
Continuing with the import possibilities the next figure shows the type of the import files/models. It is quite evident that the most frequently used import format is the dxf. (line model) file. The reason for that is most probably the simplicity of this format and accordingly the compatibility with almost all other software tools. However, this is the lowest level of interfacing option. More and more users receive their initial model from a detailing model file, which is a much higher-level import possibility, these models usually include the full member properties (material, cross-sections, eccentricities). The IFC format is also used but less often, because this type of format is not always suitable for the right definition of analysis models. Also important that the starting structural model in Consteel practically never received from another analysis and design software.
Once the members of the structural model are available, the model should be supplemented by the mechanical objects making the model suitable for structural analysis and design (supports, member connectivity, eccentricities, loads etc.). These additional modelling elements are predominantly created in Consteel, however, there are some (and hopefully growing number) users applying one of the several scripting options available (Descript – in-built scripting environment, Pangolin – scripting in Grasshopper) – see the next figure. We strongly think this is the future way of modelling making this process much more efficient and flexible to changes.
Modelling the connections
In the analysis and design of steel structures, the connections have usually great importance. First of all the design of the connections can take a considerable part in the whole process and sometimes the behaviour of connections has significant importance on the analysis and design of the structural members. From the next figure, it is clear that only a very small portion of the users are not designing the connections together with the main structure. Among the three types of applied tools, the most frequently used option is the inbuilt design tool of Consteel. It covers most of the connection types by standard calculations and has a complete interaction with the main structural model by automatic geometry, loading and stiffness transfer. There are more and more specific tools, used for the connection design, these are usually used for the design of more complicated and irregular connections. However, a considerable number of engineers are still using hand calculations or own developed Excel spreadsheets for connection design.
Exporting the results
After performing all the necessary analysis and designing or optimizing the structural elements there will be a model stage – at least in a certain phase of the design workflow – which provides inputs for the forthcoming design activities (like additional or supplementary analysis and design, detailing of the final structure, etc.). There are usually two types of supplying data for further work: (1) exporting certain numeric part of the calculation results, (2) exporting the whole structural model.
Exporting the calculation results
In the next figure, it can be seen that three-quarters of the users need to supply their calculation results to input additional calculations. It again proves the increasing fragmentation of the workflow by using specialized software for different calculation needs and the necessity for collaboration between these tools. It should be noted that the export of the pure calculation results (without the model) is a low-level workflow, compared to the whole model export (possibly including the necessary results). But this data provision is still heavily used due to the non-existing or insufficient communication between the different calculation software models. The format of the calculation results export is dominantly the forms of Consteel documentation which can be easily transferred to Word. Also, the tabular numeric results are exported to .csv as a simple and easy interface with many specific supplementary calculation tools.
The purpose of the calculation data supplying is generally the foundation and the connection design. These design topics are usually efficiently handled by specialists with specialized software tools.
Exporting the whole structural model
A more complete data provision is when the whole calculated and optimized model is exported to other applications. During the design work, the need for complete model exchange with other calculation tools can arise frequently. As it was mentioned earlier it is usually the least resolved issue since the very high number of different analysis and design packages and tools with generally no complete and sufficient direct model exchange possibility and no widely accepted and used specific central database (like IFC for architecture and BIM). That situation is illustrated in the next figure showing that the manual model building (or some other but independent model creation) in other applications is still dominant. But here again, there are signs of use of modern technics with some way of direct or indirect model exchange (sometimes through an intermediate neutral software) and 10% use a (usually own created) central data model for the import-export.
When the structural optimization is finalized – at least in a certain phase of the whole project – the finished model together with its calculation results is the most important documentation of the design work. This final model is a valuable source for the further work phases, these are illustrated in the next figure. While one-third of the users do not use the model for final data export (they use only the model and result documentation) the others export the final model mainly for the detailing process or visualization supplementing the documentation.
Conclusions
A comprehensive survey was made with the users of Consteel on their usual workflow in the structural design. Considering the characteristics of the respondents and project types, it can be seen, that we are in the middle of a big change in the structural design workflow. This is obviously supported and also constrained by the available solutions and tools. While there is still a significant portion of engineers using the old ways of structural design workflow with separated use of software tools supplemented by significant manual calculations; a considerable group is open to the modern methods governed by model parametrization, scripting methods for custom modelling and optimization and interfacing between different software solutions.
Thanks for the contribution to this survey goes to Strenco, Ergocad, Construsoft, Consteel Deutschland, and Gordias!