Introducing the 2nd place winner of The Steel Lion Award 2024. The project describes the design and dimensioning of a pedestrian bridge support structure. The project was created by Kornél Kiss, Structural Engineer, collaborator of Eurostatik R Engineering and Construction Ltd.
GENERAL DESCRIPTION AND BACKGROUND
The client was looking for a solution for pedestrian traffic in their existing production halls, separated as much as possible from forklift and truck traffic in the yard.
The enclosed, heated bridge starts from a staircase and leads to the roof of the next building. An open, steel-framed walkway bridge connects to an open walkway podium, also steel-framed, on the existing roof. From the roof, the enclosed walkway turns away, above the walkway between the two large hall buildings. The corridor on the upper floor will be built on top of and above the existing process corridor. At the end of the technological corridor, a staircase will be constructed to allow access to the ground floor and the courtyard area. After the staircase, the walkway continuing the first-floor level will lead to the first floor of the office building. A reinforced concrete slab floor with trapezoidal slabs will be constructed along the entire length of the corridor.
In designing the geometry, the architects had to deal with the height differences between the incoming and outgoing levels of the structure, which had a major impact on the supporting structure. The high, low and turning points are the main critical nodes of the structure.
Furthermore, one of the client’s important requirements was that the individual production units should be as large as possible, to minimize disruption to internal and external traffic during the construction process.
Loads and effects were defined according to the standard.
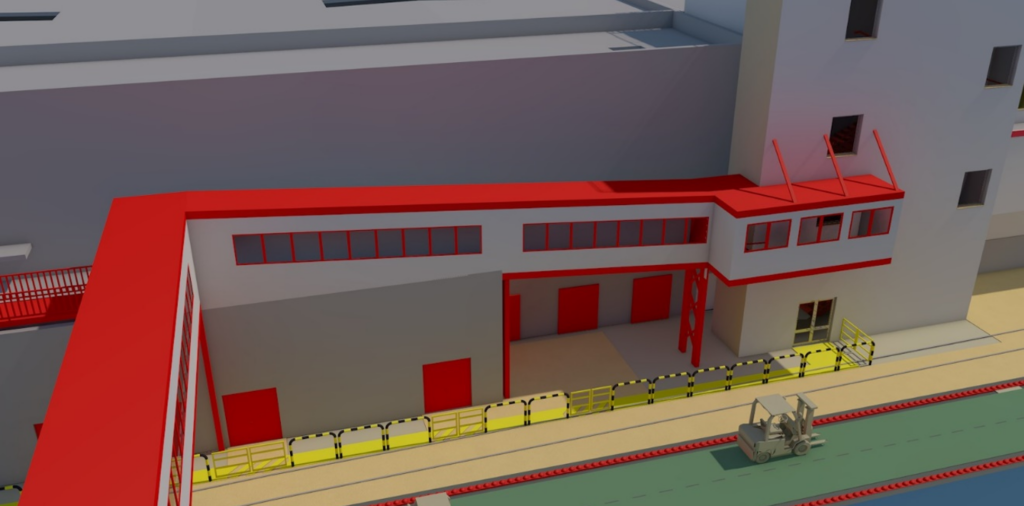
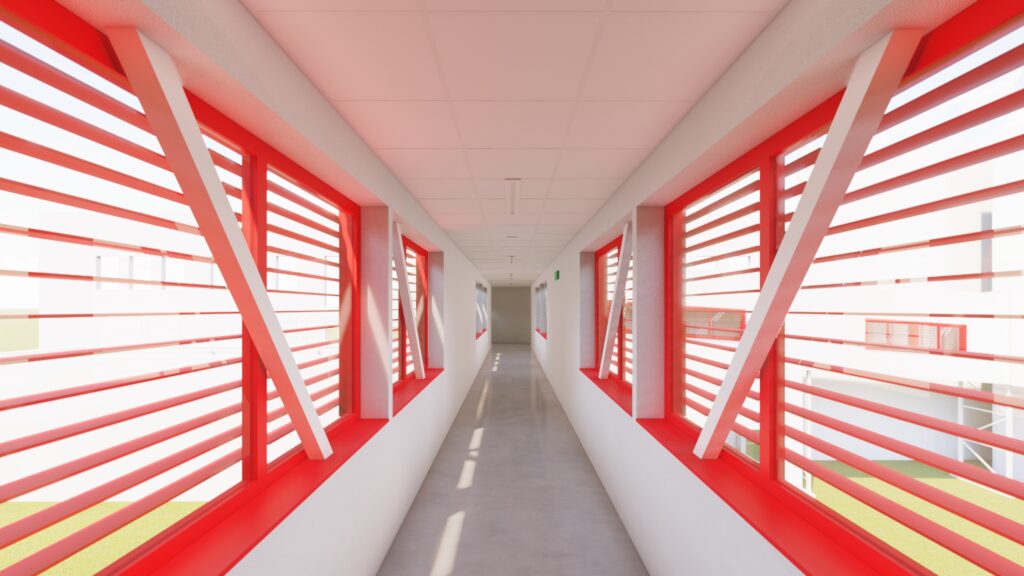
CREATING A CONSTEEL MODEL
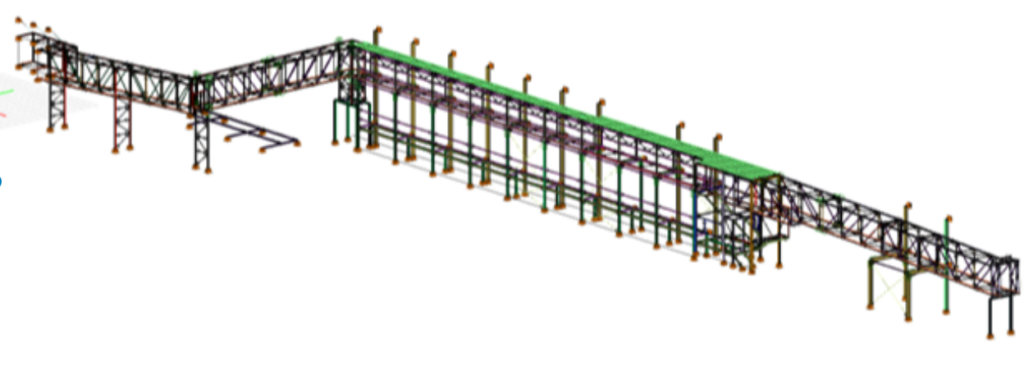
The main input data was the geometry taken from the architect and a geodetic survey of the existing and associated structures. The first, still “rough” geometry was created in Advance Steel, it was important to finalize the geometry and communicate with the designers.
Once the geometry was finalized, the Consteel model was created using an IFC file, which was successful with surprising accuracy and minimal deviations (gap between bar memebers).
The structural design was carried out using both Consteel and Advance Steel software. The sections were designed in Consteel. The selected sections were then transferred back to Advance Steel for connection design, after which their feasibility and effect were checked again in Consteel.
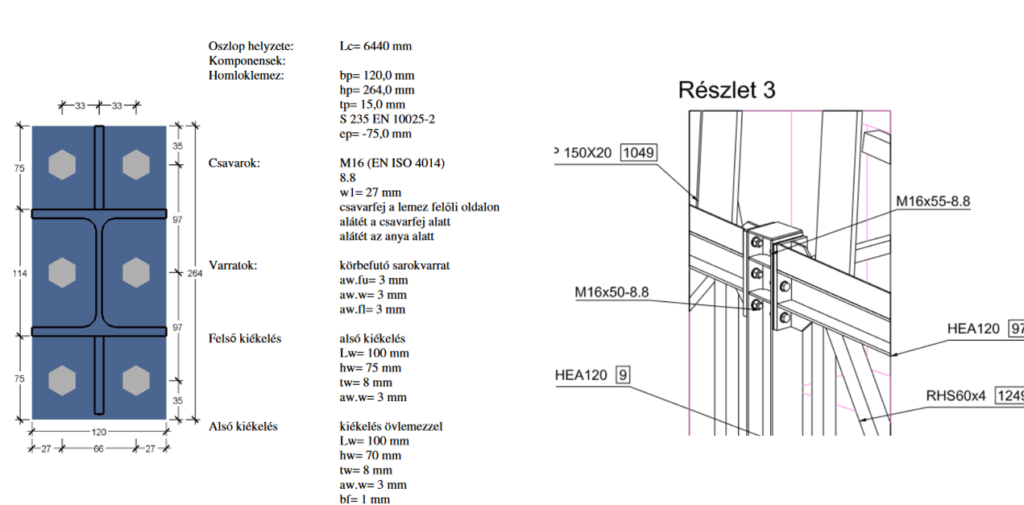
THE CONCLUSION, PLANS AND THE OUTCOME
The design duration was 2-3 months, with 1 structural engineer designing the steel structure and 1 structural engineer designing the foundations.
With Consteel, the structural complexity could be easily understood. Using software tools such as buckling sensitivity, effect and design of purlin lines, and finally checking the design of the main connections, the influence of connections’ rotational stiffness on the structure simplified the process.
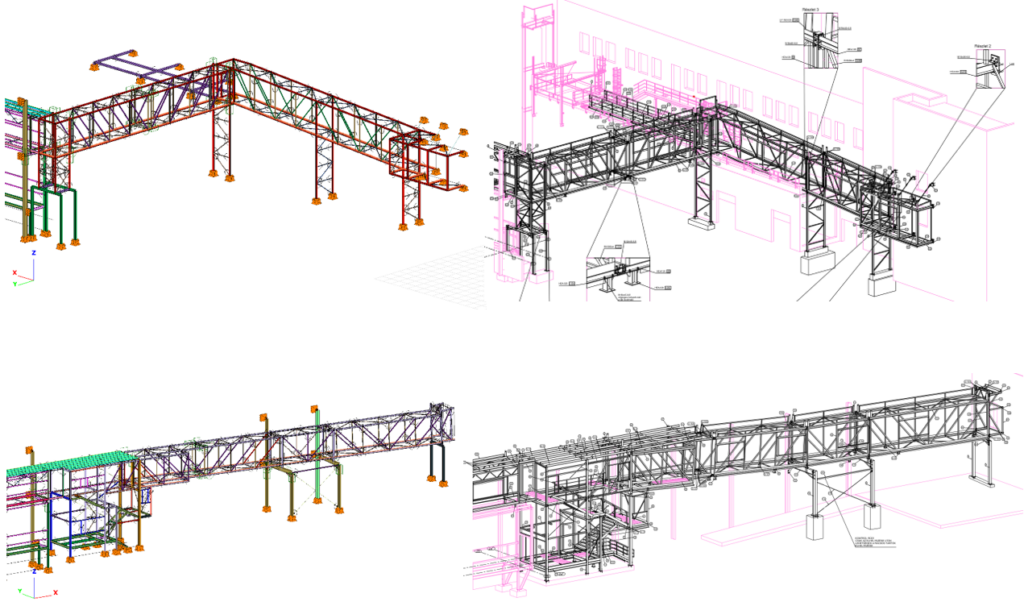
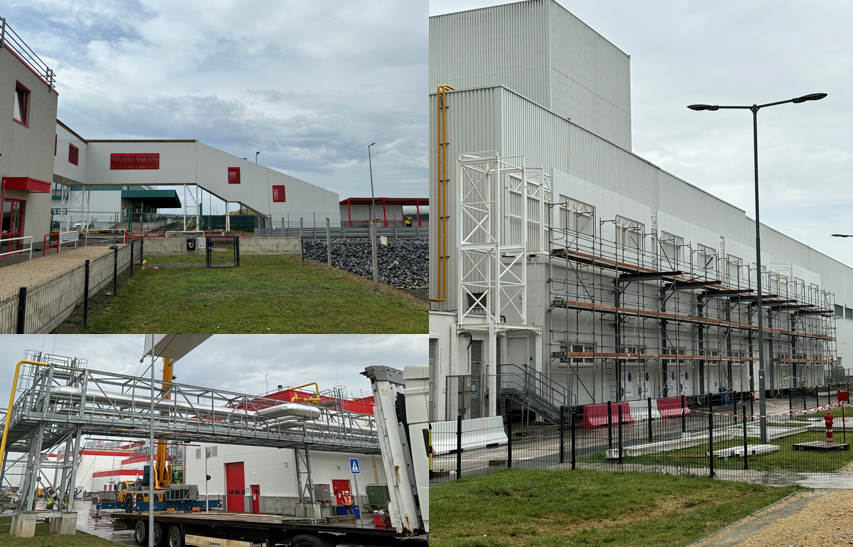
If you want to get inspired by the work of other submitted Structural Engineers, take a look at all projects on the website of The Steel Lion Award.