This time, we will take a look at the pioneering technologies used and developed by one of our customers, as well as the implementation in Consteel software for the structural design process, which has allowed them to evaluate and design to the significant loads that a solar panel support structure can be subjected to. The benefits of using Consteel in terms of workflow and productivity will also be demonstrated.
Array Technologies (STI Norland) is a company founded in Spain dedicated to the construction and implementation of photovoltaic utilization projects, including both tracking systems and fixed systems. In 2002, it built the world’s first solar tracking plant in Navarra.
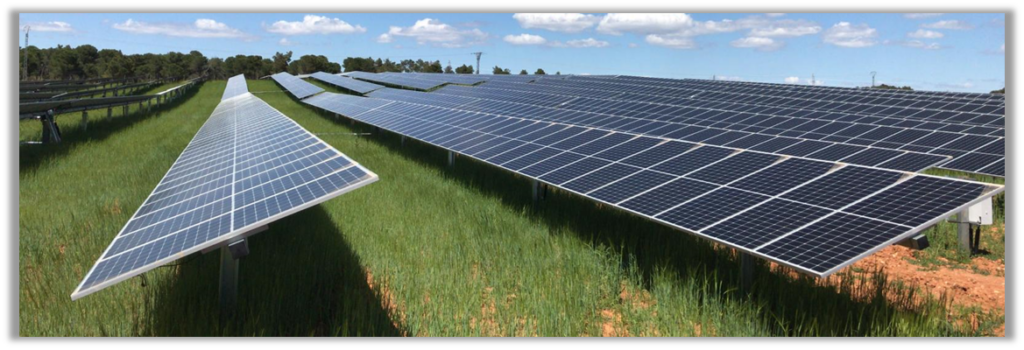
PROJECT DESCRIPTION
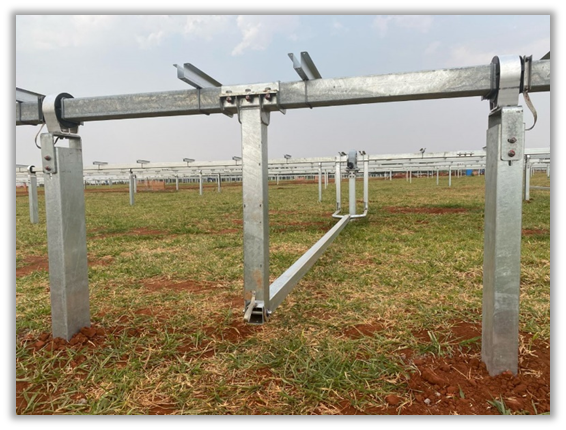
Located in Alfajarín, in the province of Zaragoza, the project involves the construction of a field of horizontal-axis photovoltaic solar trackers. It consists of two torsion beams that support the modules. This beam allows rotation through a transverse mechanism that moves the modules in an east-west direction, following the sun’s trajectory.
The oscillatory movement of the solar modules is calculated using an astronomical calculation algorithm, which also takes into account potential shading between adjacent rows of modules, thus avoiding it and increasing energy production by up to 5%.
The project is situated at an altitude of about 380 meters and consists of 29 photovoltaic modules per row. Each module weighs 32.3 kg, so each line must support a total of nearly 950 kg, distributed along it. This weight only accounts for the equipment load, not considering the significant wind pressures generated over a surface area of approximately 2.5 m² per photovoltaic module, which can amount to a little over 74 m² of surface area of photovoltaic panels per row.
CONSIDERATIONS
The analysis was primarily focused on the effect of wind loads due to their significance compared to other loads. Initially, since the structure is relatively light, it is not susceptible to the inertial effects caused by earthquakes. Snow loads were not analyzed because the tracker is designed to operate with a stable snow layer of approximately 10 cm thickness. Additionally, the oscillatory movement prevents the accumulation of a thicker snow layer. The tracker also has a snow sensor that constantly measures the snow thickness; when it reaches 8 cm, the tracker moves into a snow safety position, angling itself at 45 degrees to help shed the accumulated snow.
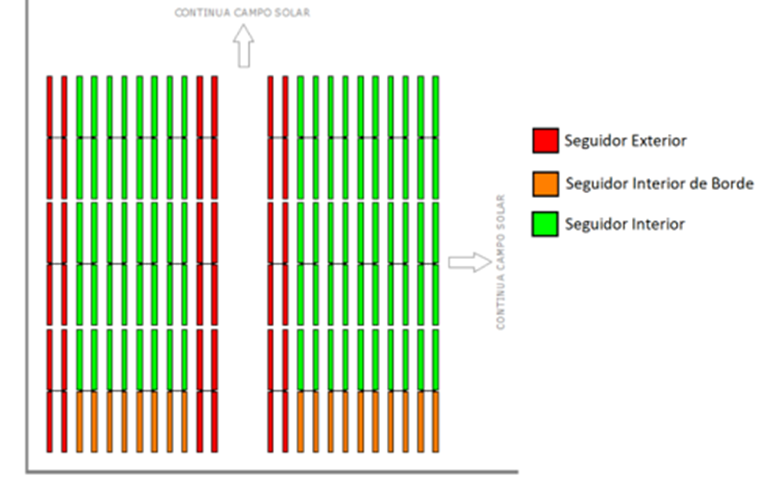
Since the constructed project consists of photovoltaic trackers, different positions of the trackers throughout the day must be considered. Additionally, different rows of modules will be affected depending on their arrangement in the plant.
As presented, three groups of trackers can be identified based on their level of wind exposure: internal trackers (Seguidor Interior), which will have a lower degree of exposure; trackers on the interior but at the edge (Seguidor Interior de Borde), which will have an intermediate degree of exposure; and external trackers (Seguidor Exterior), which have a higher degree of exposure.
Finally, by considering the permutations between the different types of trackers, their positions throughout the day, and the wind direction, we have the following possible cases to evaluate.
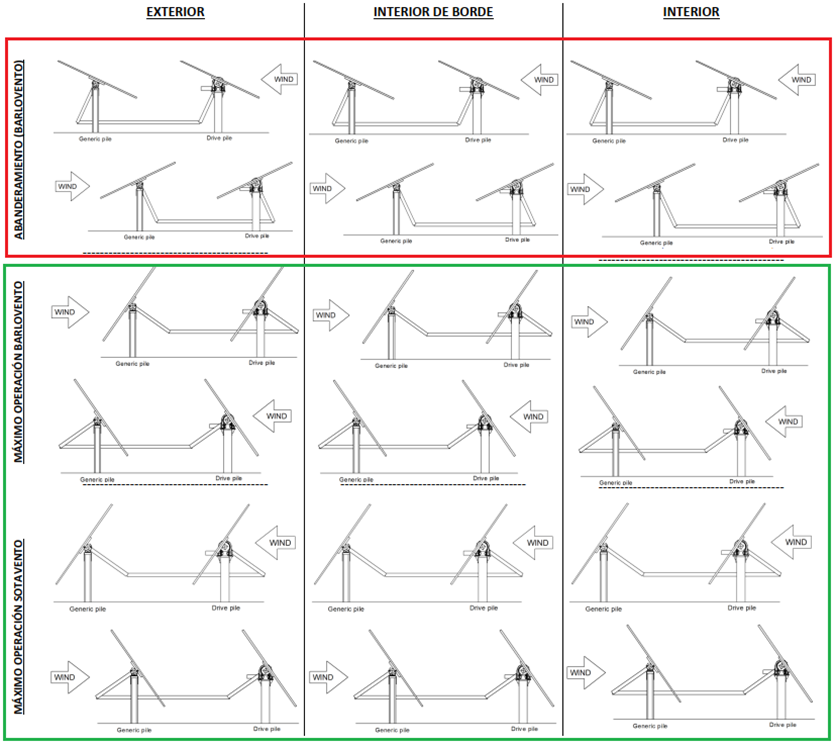
The case when the wind is from “behind” is not considered because the tracker is equipped with an anemometer. When wind speeds exceed 60 km/h, which is the design speed, the tracker enters in a position to face the wind. In this position, the structure experiences significantly less stress, whereas “behind” wind at these speeds can lead to various types of aerodynamic instabilities, which would compromise the integrity of the modules.
Given the sensitivity of the possible results, the cases can be reduced to only those highlighted in red, which represent the frontwise wind scenarios. Ultimately, the design is governed by the most exposed trackers, so the design case would be the frontwise wind, specifically for the external trackers.
MODELING IN CONSTEEL
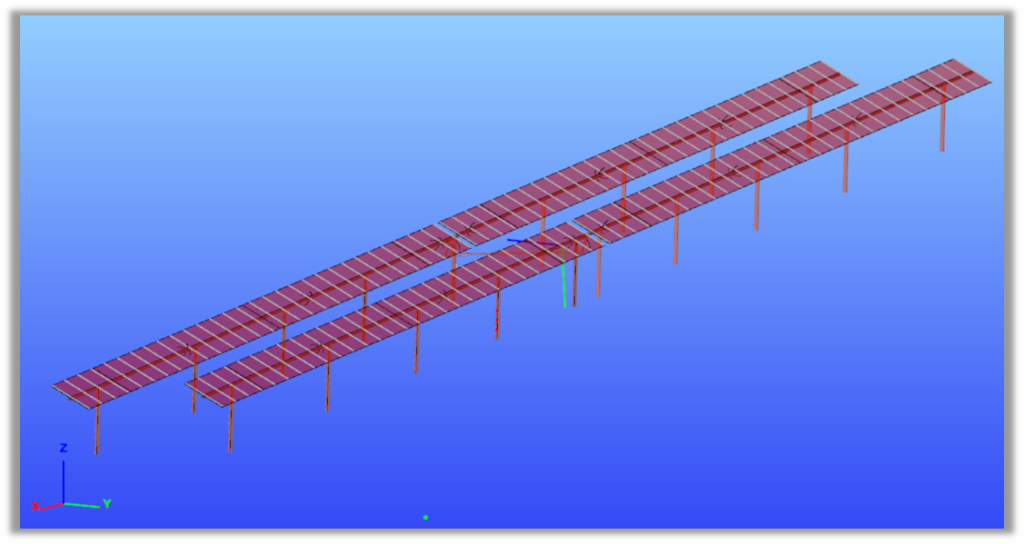
At Array Technologies (STI Norland), there are technical sheets containing all the specific dimensions of these structures. Using Descript, the internal scriping language of Consteel these sheets were the inputs to read and generate an initial geometry in the software, which speeds up the workflow in the modeling phase.
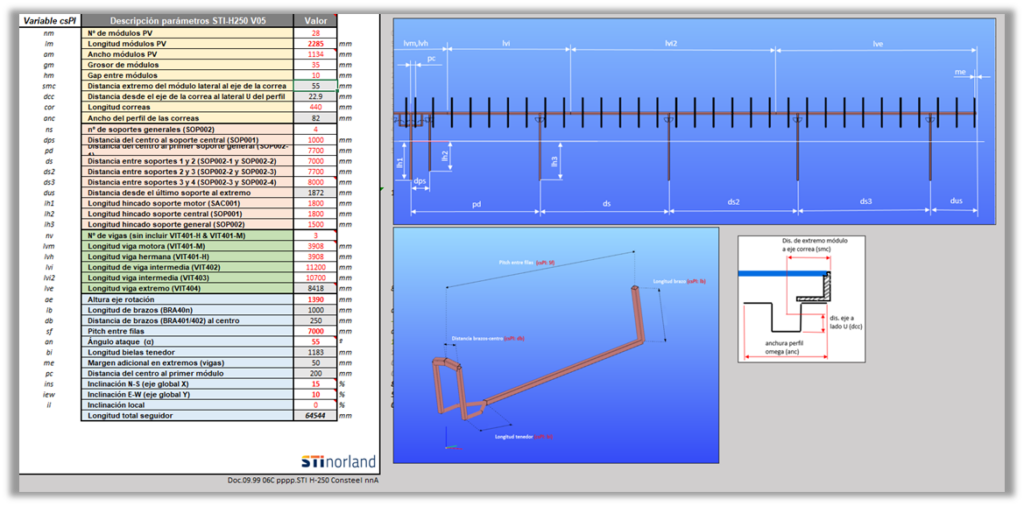
The algorithm developed by Array Technologies (STI Norland) in Consteel allows for the introduction of the corresponding loads onto the model. These loads are applied to the panels and consider the following aspects:
- Wind pressure on the panels, calculated using coefficients obtained from wind tunnel tests.
- Self-weight of the panels as specified by the manufacturer, including an additional amount to cover the weight of the cabling for panel installation.
- Self-weight of the structural elements.
The model includes the support structure where the photovoltaic modules are anchored, the torsion beam that holds all the panels, and the columns that connect these to the ground. Additionally, the model also includes the transverse mechanism that rotates the torsion beams to allow the panels to follow the sun’s trajectory.
THE VIRTUES OF CONSTEEL
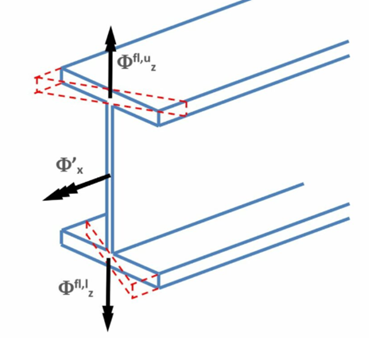
Among the most important virtues that Array Technologies (STI Norland) has highlighted in Consteel is its finite element modeling with 7 degrees of freedom. This capability allows for the consideration of stresses generated by warping in open profiles, which is crucial for structures susceptible to torsional and warping effects.
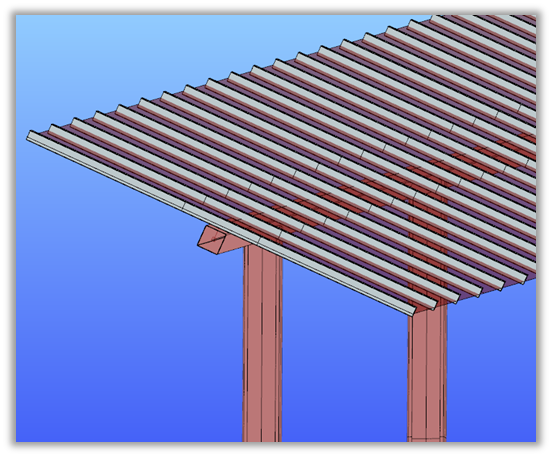
Another important aspect to mention is Consteel’s advanced handling of eccentricities between bars. This feature allows for accurate consideration of the influence and transmission of loads and deformations, not only recognizing the center of gravity of the profile but also the center of shear forces in open profiles. This capability enables Consteel to accurately reproduce the global behavior of the structure.
Additionally, Consteel allows for the determination of the global buckling modes of the structure (considering the 7 degrees of freedom) to accurately assess the buckling lengths for both flexure and torsion, even in elements with partial restraints, such as top-fixed purlins.
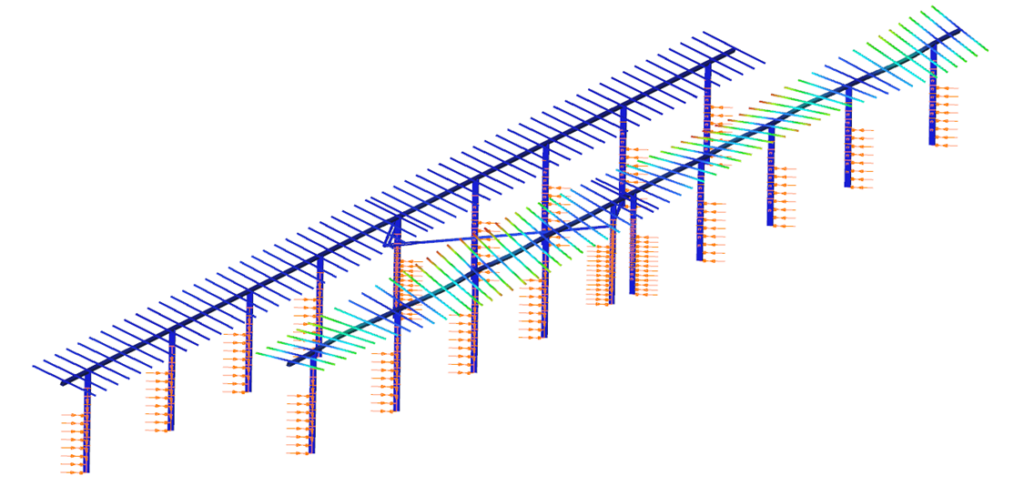
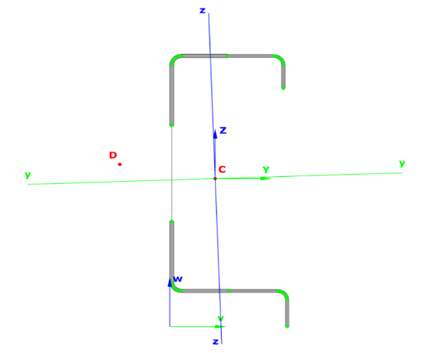
Perhaps one of the most powerful features of the program is its detailed analysis of cold-formed sections or Class 4 profiles. Consteel allows users to define any geometry using a special interface, and the software automatically calculates all the effective properties of the profile for each load combination and along the length of the bar, as these properties depend on the stress configuration in the section.
The software also stands out for its ease of use compared to other tools in the same field, and the high-quality graphical views provided during modeling. This feature allows users to get a clearer idea of the actual arrangement and the final result of the design. The importance of 3D modeling is emphasized, as it is the initial input for an analysis and modeling program, helping to ensure that the design is accurately represented and understood.
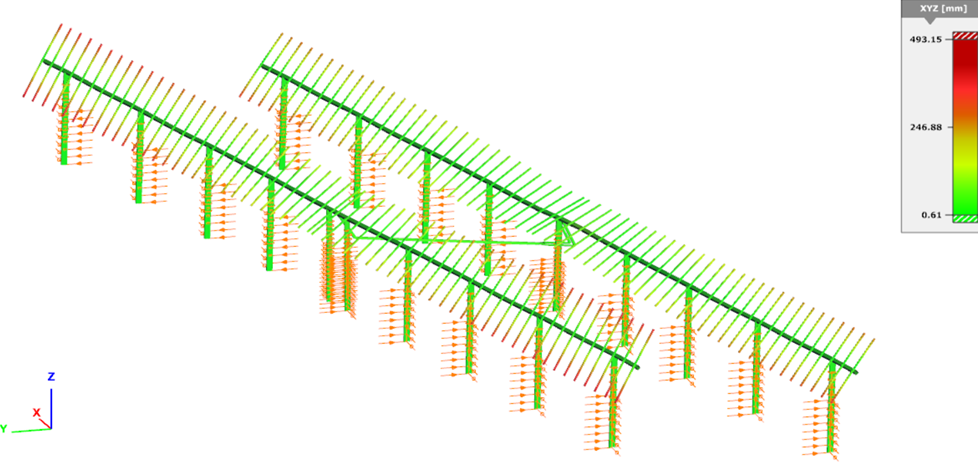